The transformer monitoring task is a complex one. Asset managers are required to monitor the health of a fleet of assets that are among the most expensive and critical to the power grid. In the past months since COVID-19 has required many people to work from home, this task has become more complicated.
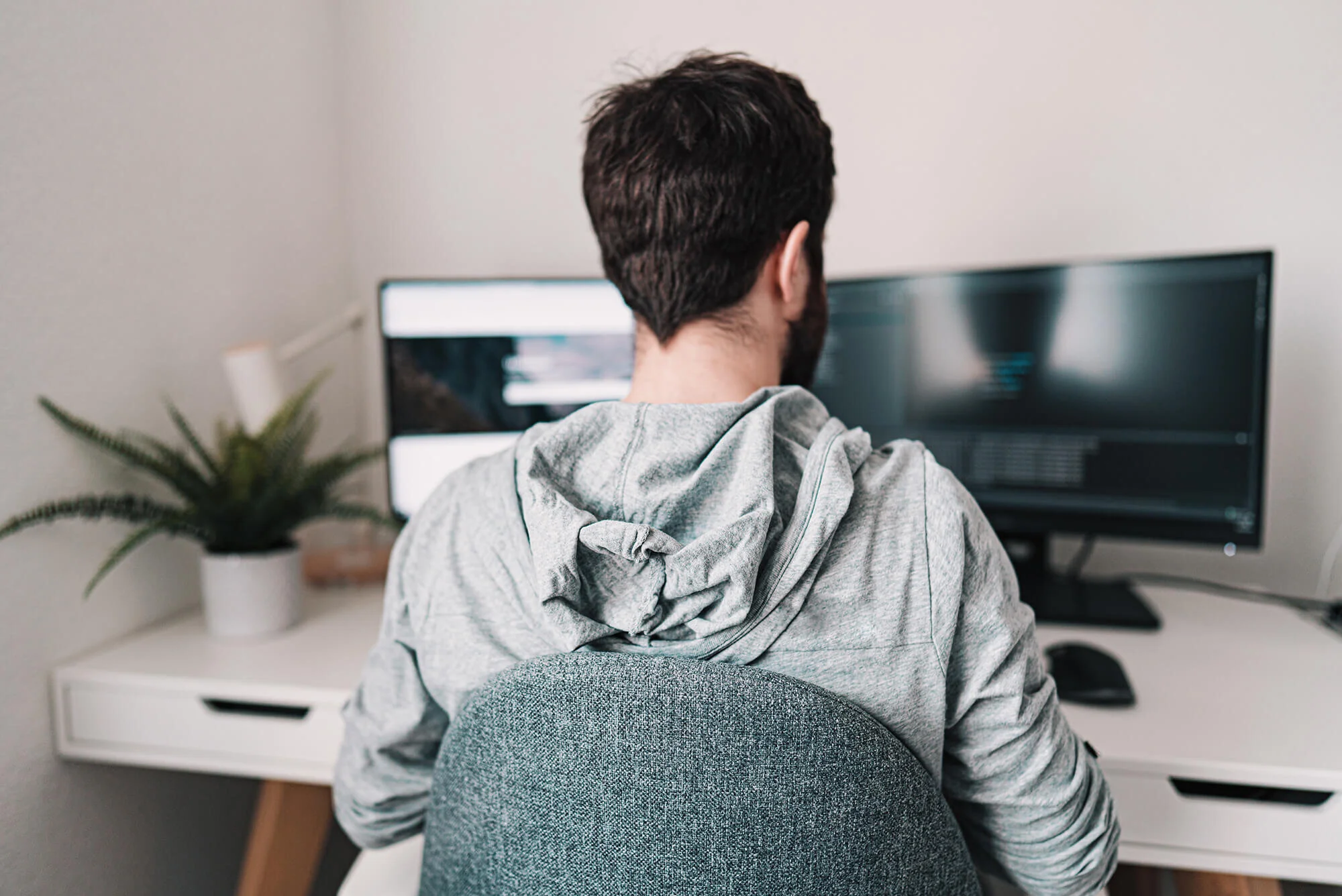
Transformer monitoring and fleet management has added complexities when trying to do this remotely - especially if you don’t have the right systems in place.
Most asset managers would have access to some level of monitoring of the health of their transformers, but most would rely to some degree on physical inspection of the asset at the substation to inspect and record/collect relevant health data. This capability has been limited for many - at the very least site visits have become more burdensome and costly to the organisation.
A recent Forbes article highlighted how not everyone can work from home. This may be the case for some transformer asset managers now - they just don’t have access to the information they need to ensure the safe operation of their fleet. They could, however, look to technology to aid them in online monitoring of a broader range of condition-based data from home. The technology exists, is available from several vendors and is always advancing. Implementing a more comprehensive remote transformer monitoring system wouldn’t happen overnight, but it doesn’t look like COVID is going to go away quickly. Nor would such a move be wasted in a post-pandemic world.
But before we take a look at some of the technology, let’s revisit the asset management task in a bit more detail and the transformer health data that needs monitoring.
The transformer monitoring challenge
Transformers are big, expensive and important assets. They have a normal life expectancy of 30 years, but can remain in operation for much longer than this. Most transformers will perform without a major fault throughout their life - and in theory wouldn’t need too much love and attention during this time. But to prevent catastrophic failure and/or major downtime for the small percentage of transformers that buck the trend, an asset manager needs to keep a close eye on each and every transformer in the fleet.
While there has been plenty of great research into why transformers fail, it remains a complex issue requiring ongoing analysis. The reasons for failure due to ageing of transformers can be identified by the following categories:
Insulation failure
OLTC failure
Winding failure
Bushing failure
Poor condition overall
To be able to identify the underlying causes of the above failures - ideally well before they happen - requires the monitoring of several key indicators of a transformer’s health - and that of it’s key components.
In addition to transformers failing due to age, there are also the cases where they suffer an untimely death in the first few years of life - an early failure - which is more often linked to a failure in the design, manufacture and/or specification of components of the transformer.
A final challenge which is particularly relevant for Australian utilities is the size of the country. Transformer fleets are geographically dispersed across a large region with a relatively small population to service. This adds another layer of complexity and cost when trying to ensure the safety and longevity of the asset fleet.
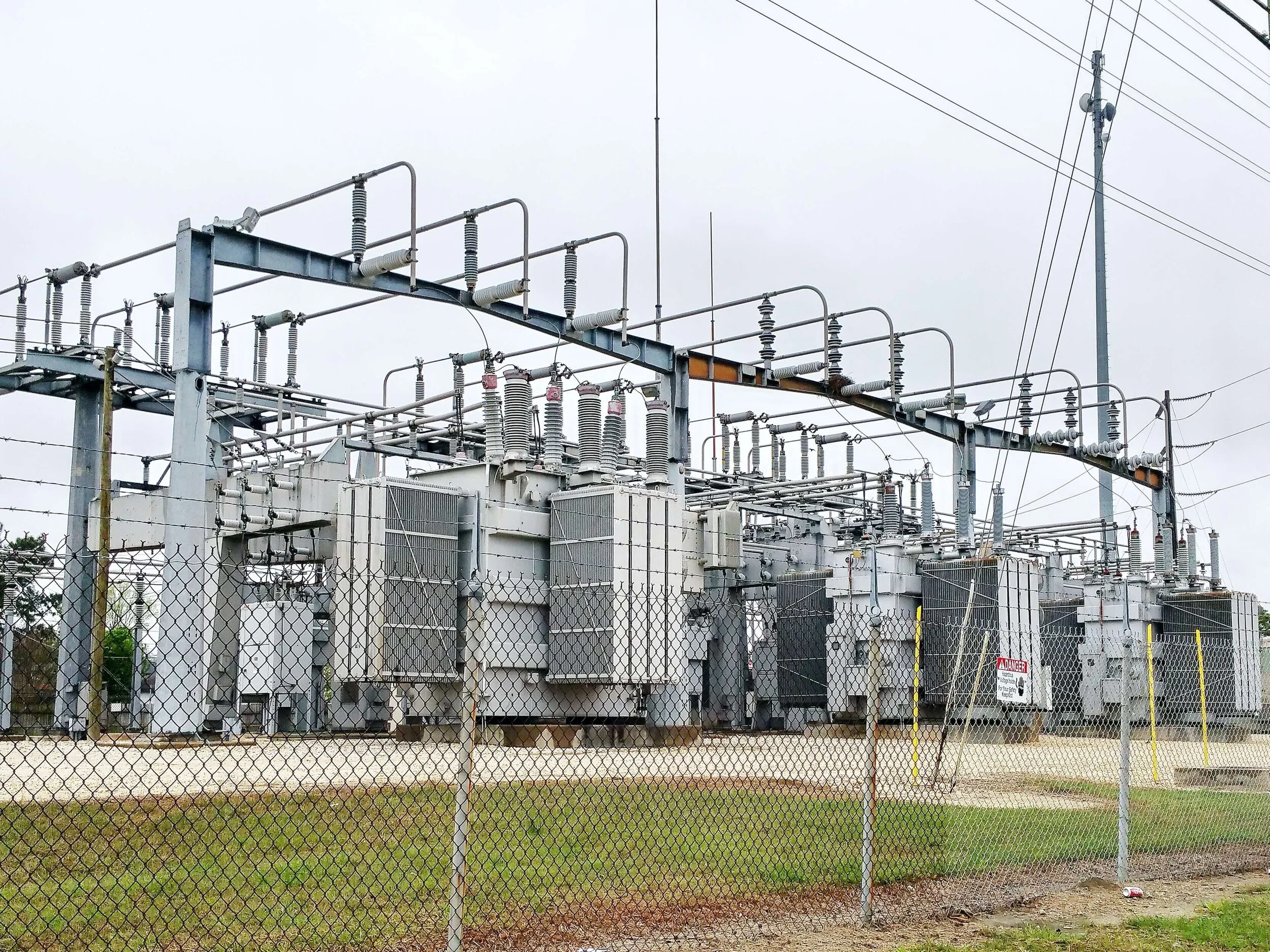
Deciding what health data needs to be monitored is one of the first steps in determining how to develop a remote transformer monitoring and management system
What transformer data should be monitored?
Each organisation will have its own asset management system in place for its transformer fleet, which defines what transformer health data needs to be captured via physical inspection and/or online monitoring. In broad terms, what can be monitored can be divided into three categories:
Monitoring specific transformer components - such as the bushings and load tap changer
Monitoring transformer condition indicators - such as temperature and moisture
Monitoring operational data of the transformer - such as the load and fan operation
One of the best ways to break down the transformer monitoring task is to evaluate what can be monitored on each of the major components that make up the transformer, as the following list and graphic illustrate.
Load tap changer (LTC) monitoring
Contact wear status
Current position and range
Tap run time and count
Motor current power
Motor actuation counter
Alarm set points
LTC temperature and differentials
Cooling system monitoring
Motor current power and motor run time
Alarm set points
Cooling bank temperature and differentials
Flow indicator status
Efficiency status
Bushing monitoring
Capacitance current value
Capacitance alarm set points
Tan delta value
Tan delta alarm set points
Temperature value
Temperature alarm set point
Leakage current value and set points
Main tank monitoring
Temperature
Pressure relief
Rapid pressure rise relay
Liquid level
Smart breather
3rd party smart sensors
Winding monitoring
Fibre optic winding temperature
Simulated winding temperature
Partial Discharge (PD)
Dissolved Gas Analysis (DGA)
Geomagnetically Induced Current (GIC)
Conservator tank monitoring
Liquid level
Buccholz relay
Bladder rupture alarm
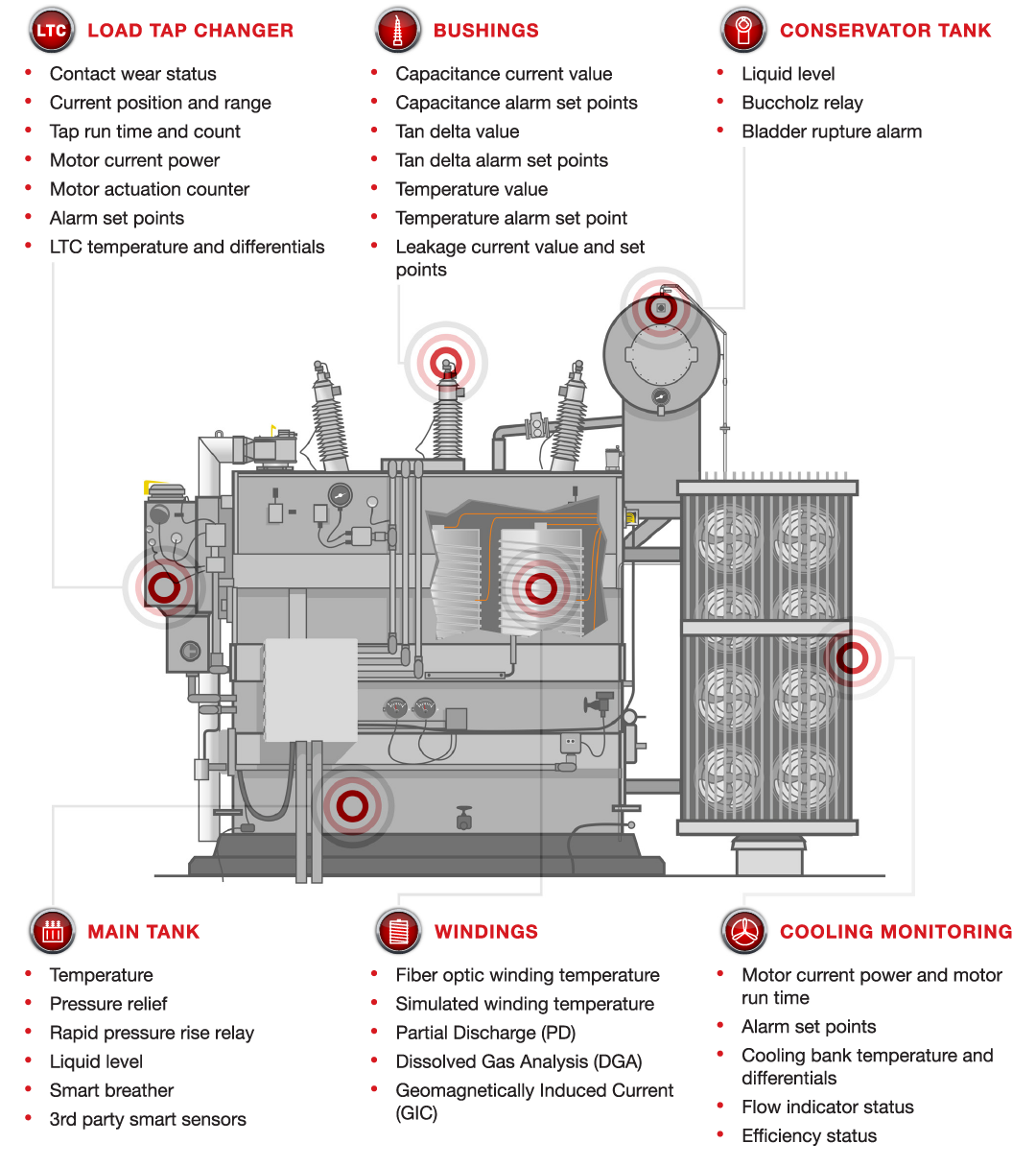
Some of the most commonly monitored data on a transformer - key components, condition indicators and operational data
The advent of “smart” transformer sensors and components
With the right equipment - measurement devices, sensors and systems - asset managers should be able to access all critical data needed to safeguard their transformer fleet. Some of this equipment has been around for a long time, hasn’t changed all that much, has been used on thousands of transformers and is highly trusted - think temperature monitoring devices like the Qualitrol AKM OTIWTI.
Various “newer” technologies emerged over the past few decades that provide more advanced insights and diagnostics, such as transformer-mounted dissolved gas and moisture analysis (as compared to lab analysis), fibre optic temperature monitoring, self-drying breathers and bushing monitors.
Many such systems have been met by engineering teams with justified apprehension and scepticism:
The ability of the devices to continuously operate in outdoor environments was unproven and no-one wants to be the first to implement large scale systems on new technology
Field trials often resulted in serious teething problems - some product or technology related; some due to poor implementation and commissioning - all viewed as failures of the technology to do its job
Integration of new sensors and their data into existing asset management systems was no small task - it would require a lot of time and resources to implement.
Over the past decade in particular, there have been significant improvements to various “smart” transformer sensors as a result of field data and experience. The latest generation of devices are more robust, reliable and worth looking at again. Below are some examples of the most recent models from Qualitrol:
That still leaves the challenge of integrating these new technologies into the existing asset management framework. That’s where smarter monitoring systems, AI and Artificial Neural Networks come in.

A screenshot from the Qualitrol TOAN enhanced diagnostics software for transformers.
Smart transformer monitoring software, AI and ANNs
One of the growing challenges for the industry is the need to provide greater grid resilience and reliability whilst facing a scarcity of resources to carry out the asset management task. In particular a lack of people with expert knowledge in transformers and condition analysis. This is where software systems can add further value by simplifying the setup and ongoing management of transformer health data.
Many software systems are already capable of the following:
Consolidate data from a large population of transformer sensors from multiple vendors
Interpret this data using industry standard diagnostic techniques, such as Duval’s Triangle
Alarm based on rate of change or absolute value thresholds
This still produces a lot of alarms and leaves a lot of data analysis to the asset management team, requiring significant expertise in this field. For example, where Duval Triangle and Pentagon requires the user to consider the intersection of various gas ratios and the resultant coordinates that the gas concentrations point to, these methods are generally employed only when certain gas limits are exceeded or when gas generation rates hit a certain defined level.
The latest generation of software - what Qualitrol have named “Enhanced Diagnostics” - go a big step beyond this by building this expertise into the software in the form of an Artificial Neural Network (ANN) and other advanced computation methodologies.
The TOAN system (Transformer Oil Analysis and Notification) is the most advanced example of this in a commercially available product. Read more about TOAN and Traditional versus Advanced Transformer Diagnostics here.
Systems like Qualitrol TOAN make it possible to design, implement and operate transformer health management systems with fewer resources and in less time.
The future of transformer monitoring
Many articles have been written since COVID hit that discuss the benefits of working from home as well as the challenges. As with any challenging situation, there are often opportunities that emerge from it. For asset management teams in charge of transformers, there is an opportunity to revisit the technology available to deliver this function more effectively and efficiently.
The smart sensors and components that make a wider set of more relevant data available
The software systems that go beyond basic analysis and alarming, to provide expert interpretation, automation and exception-based reporting.
Whilst any changes to a comprehensive asset management system will still take time and careful planning, the task is being made easier thanks to recent developments in technology.
And though we’re discussing this topic because of asset management teams who are stuck at home, all of this remains relevant in a post-pandemic world, where expertise is becoming scarcer and the need for greater resilience and reliability in the grid continues to grow.
For more information on this topic or any of the Qualitrol products and systems, reach out to our team.