Company | AusGrid |
Location | Sydney, Australia |
Timeline | 2024 |
Project Overview | Replace indoor wall mounted 132kV Disconnectors and Earth Switches located in four different transformer bays. This required four different engineered solutions from Insulect to cater for variations between the bays. |
Products |
|
Scope |
|
Complete project management & delivery
The Indoor 132kV Disconnectors Replacement project for AusGrid in Sydney was a comprehensive undertaking that involved several critical phases to ensure the successful upgrade of essential electrical infrastructure. The project commenced with a thorough site inspection and assessment, which was crucial in understanding the existing conditions and identifying any potential challenges. This initial phase involved detailed evaluations of the current disconnectors, the surrounding environment, and the overall system requirements. The insights gained from this assessment informed the subsequent stages of the project, ensuring that all aspects were tailored to meet the specific needs of the site.
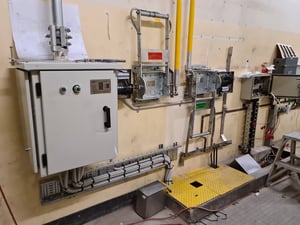
Following the site assessment, the project moved into the equipment specification and design phase. This involved the meticulous selection of disconnectors that would not only meet the technical requirements but also enhance the reliability and efficiency of the electrical system. The design process was collaborative, involving engineers and technical experts who worked together to develop solutions that were both innovative and practical. The technical drawings were then developed, providing a detailed blueprint for the manufacturing and installation processes. These drawings were essential in ensuring that all stakeholders had a clear understanding of the project scope and specifications.
The next phase involved the manufacture of the equipment, where precision and quality were paramount. The disconnectors were produced in a state-of-the-art facility, adhering to stringent industry standards to ensure durability and performance. Once manufactured, the equipment underwent Factory Acceptance Testing (FAT) and routine tests. These tests were critical in verifying that the disconnectors met all specified requirements and functioned correctly under simulated operational conditions. The successful completion of these tests provided assurance that the equipment was ready for deployment.
Logistics and transportation to the site were carefully coordinated to minimize disruption and ensure timely delivery. This phase required meticulous planning to navigate the complexities of transporting large and sensitive equipment through urban areas. Upon arrival at the site, the installation supervision phase commenced. Expert teams oversaw the installation process, ensuring that each component was correctly positioned and integrated into the existing system. This phase was crucial in maintaining the integrity and performance of the electrical network.
Finally, direction-call support was provided throughout the project to address any unforeseen issues and ensure seamless communication between all parties involved. This support was vital in maintaining project momentum and ensuring that any challenges were swiftly resolved. The successful completion of the Indoor 132kV Disconnectors Replacement project not only enhanced the reliability of AusGrid's infrastructure but also set a benchmark for future projects in terms of efficiency and effectiveness.